The two most common methods used to trigger a thermal shutoff, eliciting a failure position in pneumatically operated Emergency Shut Down and Emergency Isolation Valves are: (1) Fusible Plugs, and (2) Plastic Tubing. Both of these techniques have been used in emergency shutdown systems for years in refining, chemical, petrochemical, pulp and paper, flavors and fragrances, semi-conductor and pharmaceutical processes. A third technology based on memory shape alloys used successfully in space and aviation is increasingly replacing fusible plugs and plastic tubing based thermal shutdown systems.
1. Fusible Plugs
With fusible plugs, excessive heat causes the brass fusible pipe plug to open, allowing air to exhaust from the pneumatic actuator. The spring force closes the valve and stops the media flow. Although used for years, fusible plugs present two drawbacks:
- When the fusible plug is triggered, the air supply is not stopped. Air continues to flow through the actuator cylinder and out the open pipe plug. This air supply increases oxygen available to fire, potentially adding to the intensity of a fire.
- When the valve assembly requires periodic testing, the Fusible Plug must be replaced with a new Plug after each test.
2. Plastic Tubing
Excessive heat from a fire causes the plastic tubing to soften, melt, and rupture. Once ruptured, air can no longer reach the actuator. When the air exhausts from the pneumatic actuator, the spring force closes the valve and stops the media flow. Although widely used, it presents three negatives:
- The flow of the air supply is not stopped and continues to flow through the ruptured plastic tubing. This air supply (increased oxygen availability) can aid in the intensity and propagation of a conflagration.
- If the valve assembly is required to be tested periodically, some arrangement would have to be established to simulate the rupture or actually heat and replace the plastic tubing.
- Plastic tubing is unreliable. The effects of ultraviolet rays, age, heat, and ambient conditions can cause the tubing to fail unexpectedly, causing expensive plant shutdowns.
3. Memory Shape Alloys – FireChek®
To avoid these issues, instrument engineers now provide greater safety and system reliability with a FireChek, which uses shape memory alloy to trigger the emergency shutdown. The memory shape alloy element senses the ambient temperature and, through a phase induction change, rapidly produces the force and motion to operate. The element is 100% reliable because the shape memory effect is intrinsic to the alloy. Shape memory alloys have performed successfully for years in military, aerospace, industrial and consumer product applications. The FireChek is superior to the aforementioned approaches for the following four reasons:
- The flow of the air supply is shut off and the actuator is vented allowing the actuator to move to, or remain in, its fail-safe position. Because the air supply is cut off, oxygen is prevented from continuously feeding a fire.
- With FireChek’s memory shape alloy the automated valve assembly can be easily and economically tested. Heat testing does not destroy the shutoff trigger. The shape memory alloy simply changes shape upon exposure to a specific heat level and upon cooling returns back to its initial shape. FireCheks can be heated with a conventional commercial heat gun to trigger it to shut off and then, after it has cooled, it can be reset by hand. No tools are required to reset the thermal trigger element.
- The FireChek has a compact and robust stainless steel body capable of reliable service in the most austere environments.
- The FireChek is FM APPROVED* which may help save on insurance for the facility. FireChek ESD assemblies minimize loss risk in pneumatically controlled process applications for liquids and gases.
U.S. refineries are discovering FireCheks on ESD (Emergency Shut Down) valves. In the following photo, the refinery is using the FireChek on their ESD valves on fuel gas lines to their burners.
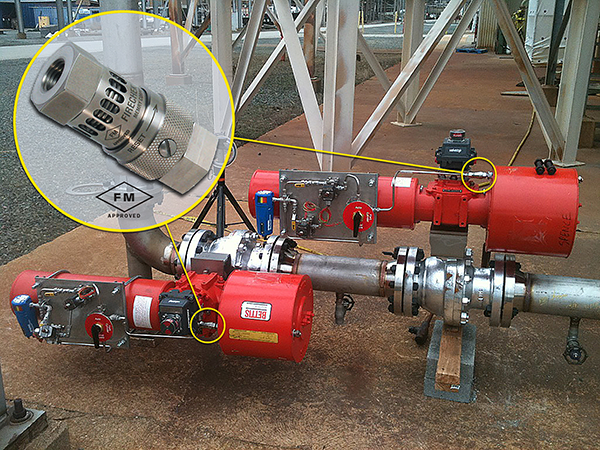
When configured with a fire safe ball valve, the FireChek thermal shutoffs function as EIV [Emergency Isolation Valves], as they fall in the class of API RP 553 Type D valves1. The fire safe valves are full port, metal seated, flanged ball valves operated by heavy-duty scotch yoke spring return pneumatic actuators. Refineries who have installed FireChek equipped ESD and EIV assemblies sought a solution to issues they had previously encountered with unreliable plastic tubing, which caused too frequent unnecessary plant shutdowns.
The accompanying photo of the FireChek installation demonstrates the simplicity of the system design.
Locations for ESD’s and EIV valves in Refinery Production Facilities (Hazard Zones) include:
- One ESD on each burner Fuel Gas or oil feed line
- On each feed line which contains a flammable fluid
- Hydrocarbon feed lines to the unit
- Lines containing toxic material if necessitated by the specific circumstances
- One ESD on each pump suction line based on size and characteristics of the inventory, as close to the upstream vessel as practical
- Install an ESD on liquid outlet line for vessels containing light ends or toxic materials
- Install ESD on liquid outlet line for vessels containing liquids heavier than light ends with their operating temperature above their flash point
- Vapor lines or vessels in vapor only service to isolate them from normal vapor path where an upset condition could lead to vessel failure Install ESD on compressor suction and discharge when horsepower is greater than 200
- Install on compressor interstage equipment when liquid inventory is more than 1000 gallons
For applications with high Cv requirements, Assured Automation is introducing a memory shape alloy based shutoff to meet the requirements of large actuators used in refineries. In addition, a field retrofit kit will be available for converting existing pneumatic actuators in the field.
While the depicted ESD/EIV valves above are in use in a refinery within a hazard zone, valves equipped with FireCheks are used effectively in other industries, both within or outside of hazard zones. FireChek thermal shutoffs are frequently used on ESD valves complying with API RP 533 Types A, B & C or similar applications and standards in other industries. They can be used on practically any pneumatically operated valve, valves with spring and diaphragm actuators, double piston rack and pinion actuators and scotch yoke actuators either double acting or spring return, either on/off or throttling. The process valves can be metal seated, fire tested or standard soft seated valves. They add safety to a wide and diverse number of process applications. FireCheks improve the reliability of triggering pneumatically operated ESD’s and EIV’s.
1EMERGENCY ISOLATION VALVE (EIV) SAFEGUARDING SURVEY, Edward M. Marshall, Kenexis, Columbus, OH and Peter G. Herena, Kenexis, Columbus, OH
*FM Approval through Memry Corp.
See article as it appeared in Valve World’s 2015 issue:
“The Pros and Cons of 3 Types of Emergency Shutdown and Emergency Isolation Valves”