Key Considerations For Effective Valve Specification
Jack Siedler has spent 43 years in the valve industry, including his current eleven year stint as a technical sales specialist with Assured Automation. During his career, Mr. Siedler has worked with bar stock globe control valves (with customized trim), rising-stem three-piece, three-way globe valves and spring and diaphragm-actuated diaphragm control valves. He has experience with sizing valves for chemical and pharmaceutical applications and has provided technical input for valve applications in the nuclear and fossil power industries. Mr. Siedler has also worked with the NAVSEA engineering group in Crystal City, Va. on valve applications for the military market. Mr. Siedler can be reached at jacks@aa-fs.com .
Q: For many applications, valve sizing and selection will determine the ultimate success or failure of the larger process. In your opinion, what are some key steps end-users can take to ensure the proper sizing and selection of valves?
JS: For the purpose of the following line of questions, let’s define the type of valves we are discussing. Years ago, control valves were generally thought of as throttling control valves. Today, however, many consider actuated on-off valves as control valves as well. For the sake of this discussion, I am going to assume we are considering both. Throttling control valves include the rising-stem type of valves, both soft-seated and metal-seated, and quarter-turn valves, both soft-seated and metal-seated with standard trim or characterized trim, coaxial, angle-seated, and diaphragm valves.
Once the appropriate type, or types, of valves for the application have been identified, the user should then attempt to determine the “approximate” size of the valve that is required. A user can effectively determine a rough valve size either by using an appropriate formula or sizing program.
Valve Selection
Regarding valve selection, users should first analyze the material of construction of the valve based upon compatibility with the media being handled. If there are a number of choices, select a few and rate them regarding their relative compatibility. The end-user is generally the best source for this determination, because in the majority of cases, it is the user that has prior experience with the media being handled, and they know more about it than anyone else. For example, the users may know the piping material that has been successful in handling their particular media. Quite often, the media is a unique mixture of chemicals. Standard chemical compatibility charts may be inappropriate for materials of construction in such cases.
Know the characteristics of the media you are handling – is it a relatively easy product to handle (air, water, inert gas) or is it toxic, corrosive, abrasive, carcinogenic; does it polymerize, solidify, crystallize; does it contain fine particulates; is it a slurry, does it have a high coefficient of expansion? All of these characteristics should be considered.
With the size, the materials of construction, the characteristics and the pressure/temperature of the media, as well as the pressure class of the piping system, the end-user can now look for the appropriate type (or types) of valve to handle the application. Armed with this information, the user can approach valve vendors for guidance in choosing the appropriate valves for the application. And once the appropriate valve has been chosen, the user can proceed to the task of sizing.
Valve Sizing
Valve sizing is the procedure of determining the appropriate flow coefficient (Cv) for the valve and the application. End-users may want to calculate the Cv required or use a particular manufacturer’s sizing program (if one is available). When sizing a valve, it is very important to use accurate information and not to make assumptions.
Some manufacturers tailor their sizing programs to the type of valves they offer. Most sizing programs utilize a simplified sizing technique. These programs have certain parameter limitations. Applications that are beyond the limitations of such programs must rely on more intricate mathematical sizing calculations. Sizing programs will likely present different limitations depending on whether the media is liquid or gas/steam.* (Please see the application data provided below for accurate valve sizing.)
In the case of throttling control valves, the customer must determine how accurately the selected valve will have to produce the determined CV. This is one of the areas where valve sizing and valve selection are interdependent.
Valve Accuracy
Although other factors may affect the accuracy of the valve assembly, throttling valve types generally fall in the order provided below from most-accurate to least-accurate:
1. Rising-stem valves (i.e., globe valves) with custom-machined all metal trim (plug and seat).
2. Rising-stem valves (i.e., globe valves) with custom-machined soft trim (metal plug and soft seat, metal seat with soft insert).
3. Rising-stem valves (i.e., globe valves) with standard all-metal trim (plug and seat).
4. Rising-stem valves (i.e., globe valves) with soft trim (metal plug and soft seat, metal seat with soft insert).
5. Quarter-turn valves with metal seats and characterized trim.
6. Quarter-turn valves with soft seats and characterized trim.
7. Quarter-turn valves with metal seats and standard trim.
8. Quarter-turn valves with soft seats and standard (full port) trim.
Valve Configuration
After selection and sizing, the valve assembly can be configured. Configuration includes selection of the appropriate actuator (pneumatic or electric) and/or positioner (if required and for throttling applications). The user must determine if the actuator is to be fail-open, closed, or double-acting. If there is a positioner, what is the control signal and are other accessories required (i.e. limit switches, solenoid valves, etc)? What size actuator is required to properly actuate the valve? If pneumatic, what is the air-supply pressure? If the actuator is electric, what is the voltage available? For electrical components, what is the NEMA rating required? These are some of the questions that generally should be addressed during the configuration process.
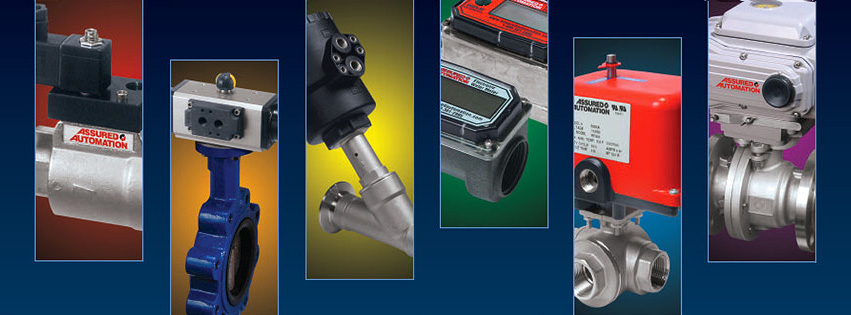