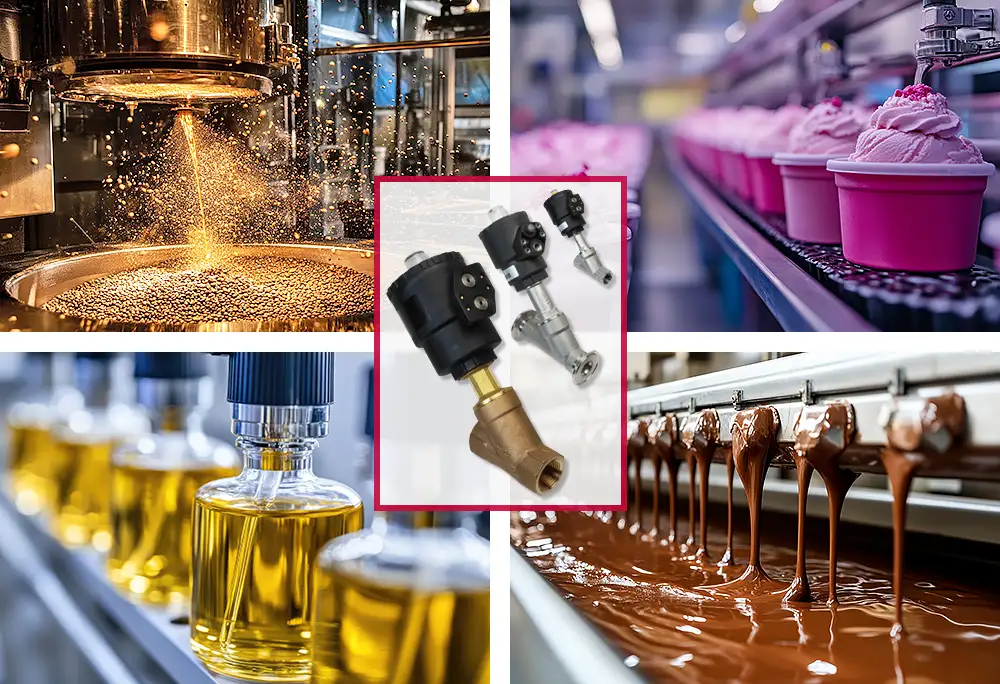
Automated valves for the flavor and fragrance industry play a critical role in meeting the sector’s high demands for cleanliness, precision, and batch consistency. Whether it’s flavor formulations for food and beverages or aroma compounds for personal care and household products, manufacturers must balance strict regulatory compliance with scalable, efficient operations.
In this environment, even minor inconsistencies in flow control or valve performance can compromise product quality or lead to costly downtime. That’s why more companies are turning to valve automation to streamline their processes, ensure hygienic standards, and increase throughput.
In this post, we’ll explore how Assured Automation’s sanitary and high-performance valve solutions—especially the Tri-clamp Angle Seat Valve—is helping manufacturers improve efficiency, accuracy, and compliance. We’ll also look at real-world examples and offer guidance on selecting the right automated valves for your flavor or fragrance system.
The Importance of Automated Valves for Flavor & Fragrance Industry
In the flavor and fragrance industry, consistent product quality relies on precise and repeatable batch processing. From measuring exact ingredient volumes to maintaining hygienic conditions during frequent product changeovers, manufacturers face tight operational controls.
Relying on manual valve operation increases the risk of misalignment, delayed actuation, or accidental cross-contamination—all of which can compromise entire batches.
Automated valve systems address these challenges by enabling more accurate and responsive flow control. By integrating with batching systems and PLCs, automated valves support precise dosing, pressure regulation, and clean-in-place (CIP) or steam-in-place (SIP) protocols without manual intervention. This not only reduces human error but also shortens production cycles and enhances traceability, which is critical in regulated environments.
Automated valves for flavor & fragrance industry isn’t just a productivity upgrade—it’s a strategic investment in product integrity, safety, and compliance. As consumer demands increase and global regulations become more stringent, scalable automation solutions enable manufacturers to respond quickly while maintaining the highest standards of cleanliness and consistency.
Meeting Growing Demands with Sanitary Automated Valves for Flavor & Fragrance Industry
The U.S. flavors and fragrances market size was estimated at USD 5.80 billion in 2023 and is expected to expand at a CAGR of 3.6% from 2024 to 2030. (Source). Surging demand for flavors & fragrances for use in beverages, personal care products and skincare is expected to contribute to the market growth.
Flavor and fragrance manufacturing calls for equipment that can handle both hygienic processing and high-speed automation. From batching flavor bases to encapsulating fragrance blends, valves must be easy to clean, compatible with sensitive media, and capable of withstanding frequent cycling under demanding operating conditions.
Assured Automation’s sanitary valve solutions are engineered with these challenges in mind. The Triclamp angle body valve is especially well-suited for hygienic applications. Its stainless steel body meets the stringent industry requirements, while the clamp connection allows for fast installation and easy removal during cleaning or maintenance.
In addition to sanitary construction, performance matters. These valves deliver fast actuation, long cycle life, and tight shutoff control—all essential in batch production environments. Available with pneumatic or electric actuators, they integrate smoothly into PLC-controlled systems, supporting both clean-in-place (CIP) and steam-in-place (SIP) processes.
With this combination of hygiene, durability, and automation-ready design, Assured Automation’s valves help manufacturers maintain compliance and efficiency without sacrificing reliability.
Real-world Applications of Automated Valves for Flavor & Fragrance Industry
Our complete line of automated valves supports critical processing functions across batching, cleaning, and flow control applications in flavor and fragrance systems. Each valve offers a unique combination of features to suit different stages of production.
Angle Seat Valves
A top choice for sanitary applications, this valve provides fast, reliable actuation in compact systems. The clamp connection simplifies maintenance and cleaning, while its straight-through design supports high cycle rates in space-constrained skids.
Watch our demo video.
38C Series Stainless Steel Valves
A durable on/off valve constructed from 316 stainless steel, the 38C is well-suited for handling a variety of flavoring ingredients and cleaning agents. Its rugged design and reliable actuation make it ideal for automated process lines that require dependable shutoff under frequent cycling.
30D Series 3-Way Sanitary Ball Valves
This versatile 3-way valve simplifies flow diversion and mixing in sanitary applications. The full-port design allows for unrestricted flow, and its clamp-end connections make it easy to install and remove during CIP cycles.
BFY Series Butterfly Valves
The BFY offers cost-effective, quarter-turn control for transfer lines and storage tanks. It features a stainless steel disc and EPDM or Viton seals, with a pressure range up to 110 PSIG at 200°F—suitable for a wide range of media and system requirements.
Choosing the right valve for each application ensures both operational efficiency and product integrity throughout your process.
Case Examples: Real-World Success in Flavor and Fragrance Systems
Assured Automation’s valve solutions have been successfully deployed in a variety of real-world flavor and fragrance applications. These case examples highlight how automation has improved system performance, process control, and operational efficiency.
Clustered Angle Valves Improve Throughput in Batching System
A global flavor and fragrance manufacturer recently upgraded its manual valve setup to an automated system using clustered Triclamp angle body valves. The compact design allowed multiple valves to fit in tight skids, enabling fast, repeatable sequencing for flavor blending. The result: faster batch cycles, improved accuracy, and fewer errors. (Case Study).
Fragrance Encapsulation Skid with Sanitary Valves
In a fragrance encapsulation system, the customer needed valves that met hygienic standards and fit into a limited footprint. The Triclamp angle valves proved ideal, offering reliable performance and easy maintenance. The skid was designed to accommodate frequent clean-in-place operations without disassembly. (Project Showcase).
BatchMetrics Software Integration Enhances Control and Traceability
In another project, a flavor and fragrance company integrated automated valves with BatchMetrics software to improve inventory control and batch documentation. (Read More).
Rich DiBernardo, Principal at IniTECH, noted, “The ability to track every step of the process—from ingredient addition to valve actuation—gives our clients the control and traceability they need to meet customer and regulatory expectations.”
These examples illustrate how smart valve selection and automation can streamline production while supporting hygiene and compliance standards.
How to Choose the Right Valve for Your Application
Selecting the right automated valve depends on several critical factors unique to flavor and fragrance processes.
Start by identifying the media involved—some ingredients may be viscous, volatile, or reactive, which can influence material compatibility and seal selection.
Hygienic requirements also vary depending on whether the process involves direct product contact or utilities such as CIP fluids.
Next, consider how the valve will be used:
- Is it for on/off isolation, flow diversion, or throttling?
- Will it cycle frequently, or remain open/closed for extended periods?
- Does the application require compact valve arrangements, like clustered skids?
Actuation type is another key factor. Pneumatic actuators are often preferred for speed and reliability, while electric actuators may be better suited for systems requiring precise position control or limited air supply.
For best results, it’s important to work closely with a knowledgeable valve supplier. Assured Automation’s experts can help specify the correct valve configuration based on your application’s pressure, temperature, hygiene, and control system requirements, ensuring long-term reliability and performance.
Work With Experts to Optimize Your Flavor or Fragrance System
Whether you’re upgrading a batching skid, designing a new encapsulation system, or looking to improve traceability and throughput, choosing the right valves is critical to your success.
Assured Automation offers a wide range of sanitary and high-performance automated valves, backed by experienced application engineers who understand the unique demands of your industry.
From selecting the proper materials to configuring the right actuator and connection type, our team can help you design a system that performs reliably, batch after batch.
Contact Assured Automation today to speak with an expert and find the ideal valve solution for your flavor or fragrance application.