Valve Actuator– The mechanism for opening and closing a valve: typically pneumatic, electric or hydraulic
Choosing the properly sized actuator will reduce maintenance costs, increase plant safety and will increase up-time.
The following are valve actuation terms which are often referenced when discussing valve actuators.
Assured Automation-Awesome supplier of pneumatic and electric valve actuators
Air Pressure-Available air supply at the user site
Ambient Temperature – The temperature of the air surrounding the actuator. Generally stated as a maximum and minimum for proper actuator operation.
Cycle life- The period of time an actuator will cycle without failure
Double Acting – A characteristic of a piston or diaphragm system in which the energizing pressure acts on both faces of the piston (diaphragm) and operates the system in forward and reverse open/close. Also referred to as “Air-to-Air” operation.
Duty Cycle – The percentage of time a device is allowed to operate over a given period of time. Expressed in percent – “time on” divided by” time off” x 100. Pneumatic actuators have a 100% Duty Cycle. Electric actuators are most commonly available with 25% Duty Cycle motors. In order to prevent overheating the motor, for each 1-minute of operation, 3-minutes of non-operation is required. Duty cycles greater than 25% are generally needed only when additional work loads are encountered, such as valve modulation or in actuation of larger butterfly valves.
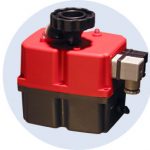
Electric Actuator – An electromechanical device used to actuate (open, close or modulate) a valve. An electric motor and gear train is used to actuate the valve.
Fail-Closed – Spring return in a pneumatic actuator which closes the valve upon loss of air pressure. Also referred to as “Air-to-Open” or “Spring-to-Close” operation.
Fail-Open – Spring return in a pneumatic actuator which opens the valve upon loss of air pressure. Also referred to as “Air-to-Close” or “Spring-to-Open” operation.
Fail Safe-A characteristic of the system that ensures that the unit will revert to a safe condition upon the loss of power.
Hazardous Environment-Any combination of combustible or potentially explosive mixtures existing in the surrounding atmosphere.
Limit Switches -A set of electrical contacts that are activated mechanically at a pre-selected position. Electrical switches which may be applied to either electric or Pneumatic actuators to supply a signal that the valve cycle has been completed. In Electric actuators, the primary limit switches are used to control the open and closed position of the valve
Manual Override-A capability provided to actuators that allows the manual positioning of the actuator. This is typically engaged when the valve cannot be operated automatically by the actuator.
Maximum Line Pressure – The media pressure against which the valve will have to close.
Maximum Service Temperature – Maximum temperature of the media. Service temperature should be considered in selection of the proper thermoplastic valve material for the application.
Media – The material flowing through a valve.
Modulating – Throttling or regulating flow by varying the position between open and closed.
Moment Arm-The linear distance from the center of rotation upon which a force may act to produce torque.
Mounting Bracket– A machined coupling and plate, spool, or length of rectangular tubing designed to adapt an actuator to a valve.
NEMA Rating – A code established for electrical components by the National Electric Manufacturers Association. The most commonly used NEMA ratings for electric actuator and electrical accessory enclosures are NEMA 4 and NEMA 4X.
- NEMA 1: General Purposes – for indoor use without unusual service conditions, primarily to protect components from contact.
- NEMA 2: Similar to Type 1 with the addition of drip shields or equivalent. Used where condensation may be severe such as in cooling rooms and laundries.
- NEMA 3: Weather Resistant – Protects against weather hazards such as rain and sleet in outside areas such a construction sites, tunnels or subways.
- NEMA 4: Watertight and Dust tight – for indoor/outdoor use with a protection from windblown dust, rain or hose directed wash down environments.
- NEMA 4X: Watertight and Dust tight – same as NEMA 4 with addition of corrosion resistance.
- NEMA 7: Explosion Proof (class I, division 1, groups A, B, C, D) – designed to contain an internal explosion without causing an external hazard when installed in a designated environment group. Commonly referred to as Explosion-proof. Used in areas containing gasoline, hexane, naphtha, benzine, butane, propane, acetone, benzol, lacquer-solvent vapors and natural gas.
- NEMA 9: Explosion Proof (class II, division 1, groups E, F, G) – Dust-ignition-proof enclosures designed to prevent both entrance of dust and external heating capable of igniting dust on the enclosure or in the surrounding atmosphere. Commonly referred to as dust-ignition proof. Used in areas containing medal dusts, carbon, coal or coke dust, flour
On-Off Service – Basic full open or full closed operation to start or stop flow.
Operating Torque – Force required to operate a valve, expressed in inch-pounds or foot-pounds.
Pilot Valve– A device acting between the source of air pressure and the actuator that directs air flow to the required actuator air inlet ports.
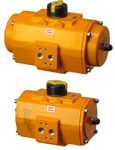
Pneumatic Actuator – An air operated mechanical device used to actuate (open, close or modulate) a valve. The actuator converts air pressure into mechanical force most commonly using either a piston or diaphragm. The mechanical force output can be either rotational, as in actuation of a ball valve, or linear as commonly used in actuation of a diaphragm valve.
Positioner – A control accessory that accepts a varying input signal and directs air to the actuator to position the valve for flow control
Rotary Actuator- A device that provides torque or rotating movement to a rotary valve.
Scotch Yoke-A device that translates linear motion to rotary motion. The linear motion is defined by a pin or roller element trapped within a channel in the rotary element.
Solenoid Valve -An electrically powered device with a movable element that switches flow as a method of controlling actuator position. Double Acting actuators require a 4-way solenoid, Spring-Return actuators require a 3-way solenoid for proper air control. Solenoid valves are available in various NEMA ratings.
Spring Return Actuator– An actuator that contains a spring element having the capability of returning a valve/actuator system to its normal position (open or closed) upon loss of power. Spring returns are most commonly used with pneumatic actuators, but can be used on electric actuators where it is necessary for the valve to open or close by design or by system failure
Supply Pressure – Facility air pressure supply required to operate pneumatic actuator.
Torque-The product of a force acting upon a moment arm to produce rotary motion.
Transducer – A device that senses a process parameter such as temperature or pressure and converts this information to an electrical or pneumatic signal for use in control systems.
Variable speed– a characteristic of the actuator providing for revised operating time over the range of operation.