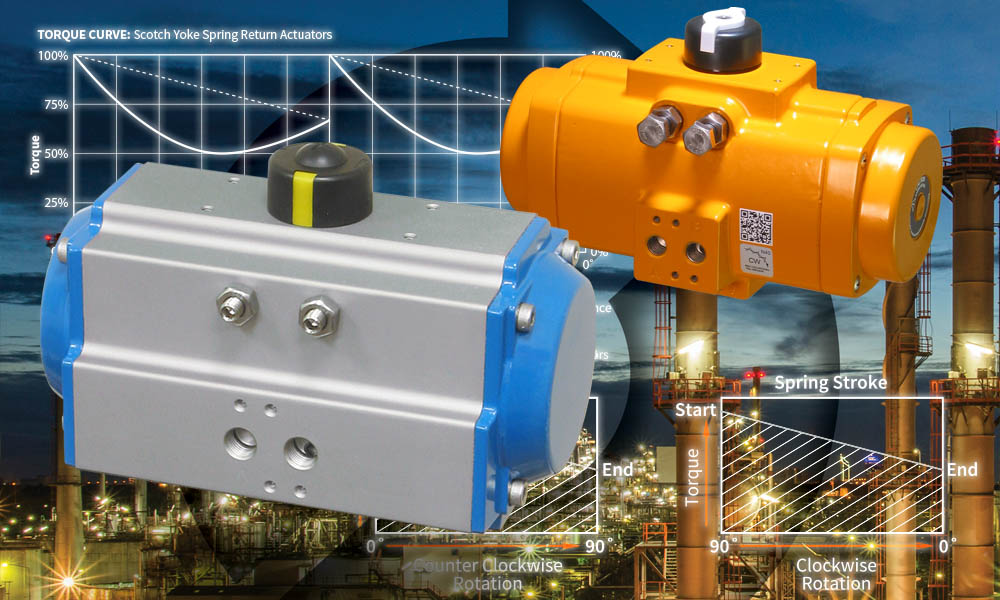
Actuator sizing for quarter-turn valves may seem simple, but there’s a bit more to it than just matching torque values from a chart against the torque values required by the valve. In fact, it’s one of the most common areas where engineers and buyers make critical mistakes.
At Assured Automation, we’ve helped customers navigate these challenges for over 40 years. This guide explains key sizing principles, how to size valve actuators correctly, what common mistakes to avoid, and how we simplify the process—with tools and support designed to help you make confident decisions.
Why Proper Actuator Sizing Matters
Actuator sizing affects how efficiently and reliably your system runs, as well as initial costs and operating costs.
Under-sizing Valve Actuators Leads to:
- Slow or erratic valve movement
- Failure to open or close the valve completely
- Delays and/or downtime in order to replace it with a properly sized actuator
- Waste of materials due to failed process results
Over-sizing Valve Actuators Leads to:
- Increased initial cost of the actuator
- Unnecessarily larger physical size and heavier weight
- Increased air consumption thus increasing the cost of energy to operate it for pneumatic actuators
- In extreme case where there are many oversized pneumatic actuators in use and/or with high cycle frequency, oversized actuators may cause the need for a larger capacity compressed air system
- Valves with oversized pneumatic actuators will take longer than needed to cycle on the air stroke – whichever direction that is
- Valves with oversized electric actuators will take longer than needed to cycle on both clockwise and counter-clockwise strokes
Actuator Sizing Basics for Quarter-Turn Valves
It’s all About the Torque:
Output of the Actuator vs. Requirements of the Valve
When sizing rotary actuators for valve applications, torque is the most important factor. For quarter-turn valves like 2-way and 3-way ball, butterfly, and plug valves, the actuator must overcome the valve’s “break torque” (the initial force needed to unseat the ball, plug, or disc) and also provide sufficient “running torque” throughout the entire stroke.
The core of actuator sizing lies in ensuring that the lowest torque output of the actuator is greater than the highest torque required to actuate the valve.
Actuator Output
IMPORTANT: Torque Output of an Actuator is NOT Always Constant!
Understanding torque curves is essential when selecting between actuator types. Scotch yoke actuators, for example, generate non-linear torque—with high torque at the beginning and end of the stroke. This makes them ideal for applications requiring extra force to unseat or reseat the valve (such as resilient-seated butterfly valves or high-pressure ball valves). On the other hand, rack-and-pinion actuators produce a linear torque output. Spring return actuators always deliver less torque at the end of the stroke. This is true on the sir stroke and the spring stroke.
Double acting rack-n-pinion actuators are the only type that have a constant
Rack-n-pinion Spring-return actuators provide linear decreasing torque in BOTH directions.
Air Stroke: As the spring compresses, the resisting force it creates increases, therefore the actuator’s torque output decreases.
Spring Stroke: As the spring expands, the force provided decreases.
Scotch Yoke Spring-return actuators provide a curved decreasing torque in BOTH directions.
Air Stroke: As the spring compresses, the resisting force it creates increases.
Spring Stroke: As the spring expands, the force provided decreases.
Both Strokes: the torque is reduced in the middle of the stroke due to the mechanics of a scotch yoke.
Valve Requirements
Quarter-turn valves operate with a 90-degree rotation to open or close the flow path. While that motion is simple, the forces required to drive it vary considerably based on valve design, media characteristics, media, and system conditions.
IMPORTANT: There Are Usually More than One Torque Value to Consider for a Valve
- Break torque (aka, unseating torque) is the initial force needed to start the valve’s rotation. This can increase considerably in applications where the valve remains in one position for an extended period of time and when the differential pressure is high.
- Running torque is the torque required to maintain the movement between its fully open and fully closed positions.
- Seating torque is the force needed to close and seat the valve completely. While this is slightly increased for ball valves, it can do so considerably for resilient seated butterfly valves.
Additional Factors That Impact Torque Requirements
Several application or system-specific variables can also influence torque requirements—some of which engineers and buyers often overlook. Here are the most critical ones to consider:
Media Type and Process Conditions
Different media can dramatically affect torque requirements. For instance:
- Dry gases lack lubricating properties, often increasing break torque.
- Slurries and viscous fluids demand more force to ensure a complete seal on closing.
- Fibrous or particulate media can create intermittent resistance that the actuator must overcome.
A higher safety factor is often advisable when working with potentially hazardous or corrosive media. It’s not just about valve function—it’s about ensuring safe operation under worst-case conditions. Electric actuators must be NEMA rated for the area classification (E.G. Nema 4, 4X, 6, 7, etc.).
Air Supply Pressure
Pneumatic actuators rely on consistent air pressure to generate torque. Assured Automation typically sizes actuators for 60 or 80 psi, which aligns with most industrial air systems. But if the supply pressure fluctuates—or drops below spec—the actuator might not deliver the torque you expected. That’s why a minimum 20% safety factor is typically built in, then adjusted upward if the other attributes of the application demand it.
Mounting Compatibility
Adhering to ISO 5211 standards is key to ensuring actuator and valve compatibility. Most components have dual- or even triple-patterned standard bolt circles to accommodate multiple sizes. Making sure that the valve and actuator share a common bolt pattern is the key for the direct mount connection.
Additional Mounting Hardware
In addition to matching the bolt circles, the stem shape, size, and height must mate properly. If a mismatch occurs, the actuator won’t fit—or worse, an improper fit could cause “slop” or “play” between components, leading to incomplete travel, stem or socket wear, and eventually failure due to stripping. Selecting correctly sized inserts, reducers, and couplings is critical to ensuring a tight, proper fit. That’s another aspect you won’t have to worry about when using Assured Automation’s actuated valve configurators.
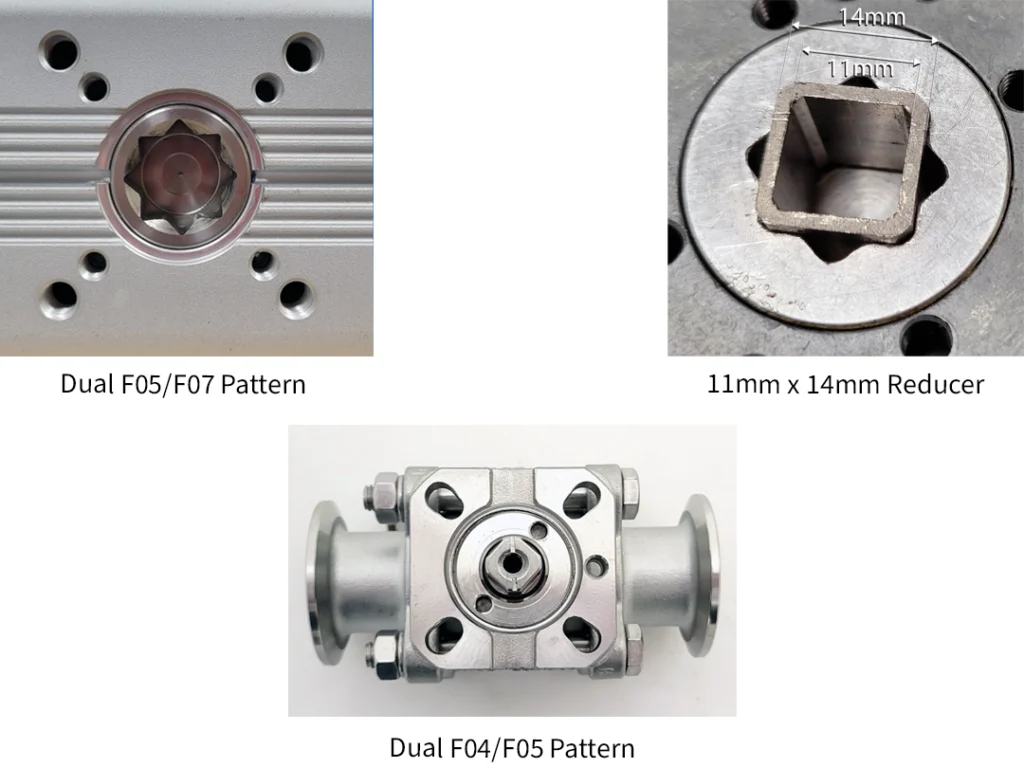
Common Sizing Mistakes (And Their Consequences)
Under-sizing is the most frequent mistake due to skipping safety factors, misjudging break torque, ignoring media effects or other special conditions. This can cause incomplete valve actuation or failure under load.
Another issue is the incorrect actuator type or configuration. Some forget that spring-return torque decreases at end stroke or that scotch yoke actuators deliver non-linear torque. Start, mid-stroke, and end torque values can be drastically different.
Mechanical mismatches like stem misalignment or incorrect ISO pattern mounting can cause excessive wear or assembly failure. Even over-sizing has consequences: excessive air use, slow cycles, or overly complex mounting.
These are avoidable with the right tools and expertise.
Special Considerations in Harsh or Complex Environments
- Hazardous Locations: Use of explosion-proof, NEMA rated electric actuators, solenoid valves, and feedback switches are required in flammable environments. Torque requirements will remain the same, but electrical specifications change.
- Extreme Temperatures: Affect seals, lubrication, and performance. Choose actuators rated for your conditions.
As you can see, quarter-turn valve actuator selection and sizing isn’t just about hitting a torque value. It’s also about accounting for line pressure, stroke dynamics, and mechanical compatibility to ensure the valve opens and closes as intended—every single time.
How Assured Automation Simplifies the Sizing Process
Use our online configurators for standard applications— select valve size, actuator type, and air pressure. The system handles the rest, including hardware selection.
Our team steps in when conditions are unusual—viscous media, fluctuating pressure, and special certifications. We match torque, patterns, and hardware to your specifications and deliver pre-assembled solutions ready to install.
We make valve automation easy! by combining tools, experience, and support.
Key Takeaways:
Correct actuator sizing impacts system cost, performance, efficiency, and reliability.
Avoid common pitfalls by considering:
- Break and seating torque — not just running torque
- Air pressure variation and safety margins
- Actuator torque curve types
- Media substance and conditions
- Mounting compatibility (ISO 5211)
For more help, refer to our Valve Actuators – Quarter-turn Selection Guide or speak with our engineering support team. Assured Automation offers live support via online Chat or Phone during Normal Business Hours EST.
For standard actuated valve packages, use our interactive valve configurators.
For complex needs, contact us—we’ll help you get it right!
- Call 1-800-899-0553
- Download our Pneumatic Actuator Brochures
- Buy C Series Rack & Pinion Pneumatic Valve Actuators
- Buy F Series Rack & Pinion Pneumatic Valve Actuators
- Buy P Series Dual Scotch Yoke Pneumatic Valve Actuators
Remember—We Make Valve Automation Easy.