The use of pneumatic and electric automation have been the life blood of industrial processes found in chemical and petrochemical plants, oil and gas processing, food and beverage processing, pharmaceutical manufacturing, pulp and paper processes, automotive and metal fabrication, and power generation. The popularity of pneumatic-based systems can be attributed to several factors, which provide many advantages over electric options:
- Fast Response: Pneumatic actuators offer quick cycle times, making them suitable for applications requiring rapid actuation.
- Durability: Pneumatic actuators are robust and can operate effectively in harsh environments, including extreme temperatures and explosive atmospheres.
- Cost-Effective: Generally, pneumatic actuators have a lower initial cost compared to electric actuators. Consequently, initial upfront costs are lower .
- Pneumatic systems are more reliable and have less moving parts which results in lower maintenance costs in the end.
- And importantly, pneumatic actuators on their own are naturally inherent from any ignition source, making them ideal for hazardous environments.
As processing plants increasingly adopt electric actuators to leverage compatibility with advanced control systems, the use of electric processing systems are increasing.
A simple decision tree, published by Brian Booth in Valve World Americas, helps engineers assess whether a pneumatic or electric actuated system is best for a given application. See https://assuredautomation.com/news-and-training/wp-content/uploads/2016/08/electric-vs-pneumatic-rotary-actuators.pdf
Industrial Fires
Industrial and manufacturing facilities in the United States have experienced a notable number of fires in recent years. According to the National Fire Protection Association (NFPA), in 2022, there were 36 large-loss fires or explosions in the United States, marking the second-highest number of such incidents in the past decade.
While specific data for industrial and manufacturing fires in 2022 is not yet available, previous NFPA reports indicate that fires in industrial or manufacturing facilities have historically caused an average of $1.2 billion in damage annually in the United States.
According to NFPA, manufacturing and industrial sites accounted for 30.5% of losses in large-loss fires in 2022 – higher than any other type of property use, including wildfires. The property losses from these fires were $530 million – that’s more than half a trillion dollars.
These statistics underscore the persistent fire risk of fires in industrial and manufacturing settings, highlighting the importance of stringent fire safety measures and proactive risk management for manufacturers.
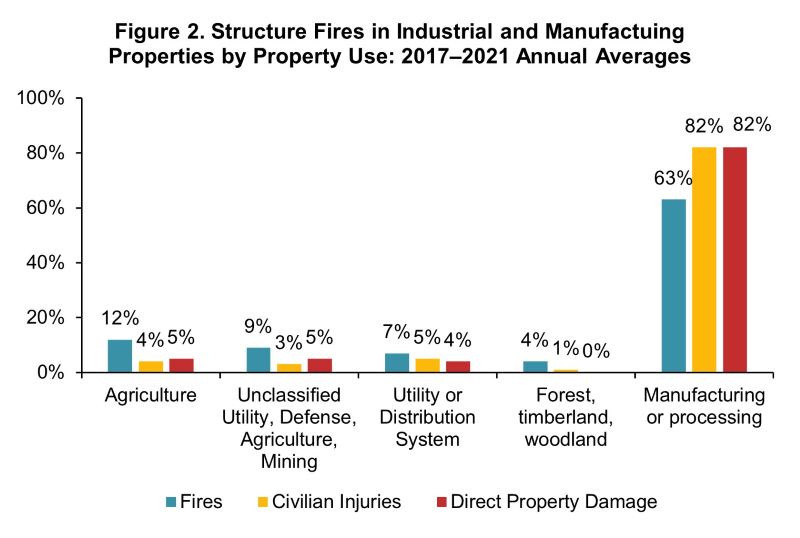
Industrial fire hazards for manufacturers may result from overheating, equipment malfunctions, and combustible materials used In the manufacturing process such as flammable liquids or gases. Thermal shutoffs play a crucial role in mitigating fire risks by automatically shutting down equipment or isolating affected areas when excessive heat is detected. These critical fire safety devices ensure that excessive temperatures do not lead to catastrophic failures. Thermal shutoffs activate when temperature thresholds are exceeded, preventing fires from escalating enabling the operation of the fire safe operation of the automated valve. They function through heat-sensitive materials that trigger mechanical or electronic responses to shut down airflow, isolate fuel sources, or activate fire suppression systems.
Thermal Shutoffs in Fire Suppression Systems
In addition to shutting down processes in fire situations, thermal shutoffs are used to suppress fires when they do occur. They are critical components in:
- Sprinkler Systems: Thermal shutoff valves can trigger water or foam-based fire suppression.
- Gas Suppression Systems: CO₂ or inert gas suppression can be activated through temperature-sensitive triggers.
Facility Zoning and Isolation
Entire manufacturing plant designs also include thermal shutoffs to isolate and limit damages, such as plant designs that include:
- Automatic Ductwork Shutoffs: Prevent fire spread through HVAC and exhaust systems.
- Compartmentalized Pneumatic Controls: Thermal shutoffs can isolate affected sections of a plant, limiting fire propagation.
The Technology Behind Thermal Shutoffs
Thermal shutoff devices can operate through several methods, including:
- Bimetallic Sensors: Materials that expand at high temperatures to trigger shutoff mechanisms.
- Fusible Links: Components that melt at preset temperatures, engaging pneumatic or electrical systems.
- Thermal Relays: Sensors that send electrical signals to shutdown machinery or activate fire suppression.
- Automatic Valves: Pneumatically controlled shutoff valves that actuate when excessive heat is detected.
Regulatory Standards & Compliance
Thermal shutoffs are mandated by various fire safety and industrial standards, which include:
- NFPA 86: Standards for industrial ovens and furnaces, emphasizing thermal safety controls.
- OSHA 1910.307: Guidelines for hazardous locations and fire prevention in industrial settings.
- ISO 13849: Safety of machinery standards, addressing thermal and operational risks.
Manufacturers must ensure that thermal shutoffs meet these regulations and undergo periodic testing for reliability.
Several excellent automatic thermal shutoffs are available on the market, for this critical safety component for both pneumatic and electric processes.
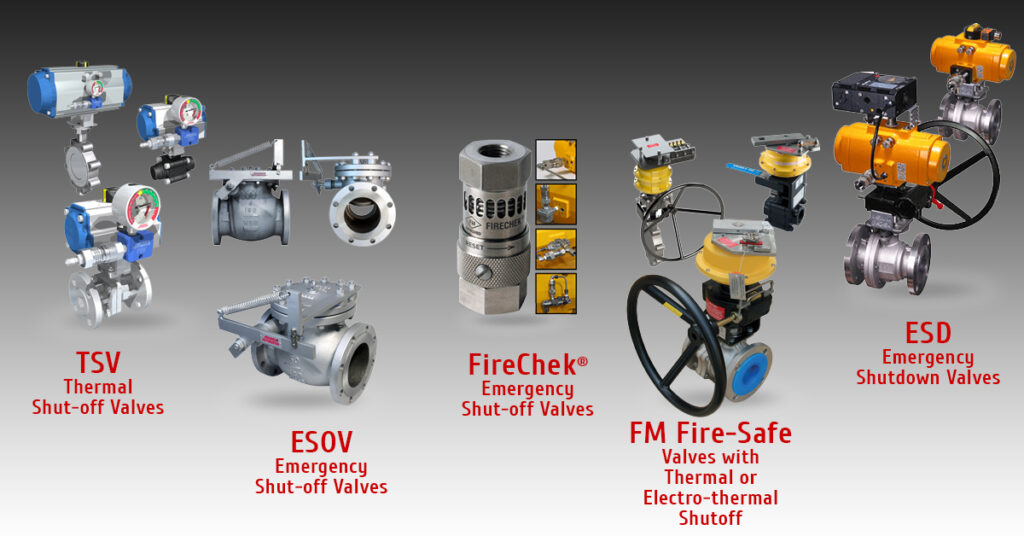
Widely adopted thermal shutoffs for either pneumatic or electric processes include:
- FM FireSafe Fusible Link Thermal Shutoff Valves are available with 3-piece ball valves, W50 Flanged Ball Valves, or BFV Butterfly Valves. All valve assemblies are Fire-Safe to API 607. U. L. Listed Thermal Links are available at trigger temperatures of 165° F (74° C), 212° F (100° C), 286° F (141° C), or 360° F (182° C), 500° F (260° C). These valves meet the National Fire Protection Association NFPA 58, (1979 Edition), OSHA 29 CFR 1910.106(b)(4)(iv)(c) Flammable Liquids, and ANSI/API 607 Fire Test for Soft-Seated Quarter Turn Valves.
- ESOV Series Emergency Shut-off Valves (Swing Check Valves with Fusible Link)
These swing check shut-off valves use fusible links to stop flow of media. They provide a simple yet effective method of closing in an emergency or hazardous situation. They can provide local and/or remote actuation, and can be configured with one of three different trigger types: either Spring Assisted with Fusible Link Only, Spring Assisted with Fusible Link and Air Cylinder trigger, or Spring Assisted with Fusible Link and an Electro-Magnetic trigger.
The assembly includes an ANSI flanged swing-check valve. The fusible link trigger temperatures are available for 135°F, 165°F, 212°F, 280°F, or 360°F.
Widely adopted thermal shutoffs for pneumatic processes include:
- FireChek®
The FireChek is preferred over thermal fusible link type valves, since the FireChek can be tested and reset after triggering, whereas a fusible links cannot. The FireChek also avoids the extra maintenance required of aging fusible links, which must be replaced periodically. - TSV Thermal Shutoff Valves are available for either fire-safe ball valves or fire-safe butterfly valves, in carbon steel or stainless steel. All seats and seals are fire-safe to API 607-5. Included in the assembly is a spring-return pneumatic actuator. The thermal shutoff assembly are available with trigger temperatures of either 165°F, 150°F, or 135°F. The thermal shutoff action is reliably set in motion by a FM approved FireChek® valve. The FireChek is preferred over thermal fusible link type valves , since the FireChek can be reset after triggering, whereas a fusible link cannot. Resetting the FireChek involves charging the actuator with compressed air through the assembly’s Schrader (check) valve to 120 psi on the gauge, which is also included in the assembly. This allows the TSV to be tested and reset without replacing hardware.
- ESD Emergency Shutdown Valves are Fire-Safe to API 607-5, and come equipped with a Spring Return Actuator with FireChek Thermal Shutoff, and a solenoid for actuator control and remote shutoff. They are available for both flange or NPT connections. Emergency Actuation Temperature options are 165°F, 150°F, or 135°F.
Thermal shutoffs play a vital role in fire safety within manufacturing plants using pneumatic systems. Their ability to prevent overheating, trigger fire suppression, and comply with safety regulations makes them an essential component of industrial fire prevention strategies.